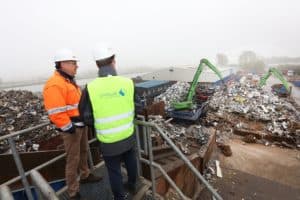
HKS Metals has equipped its shredding system with system components made by Cyrus GmbH Schwingtechnik. The vibratory trough conveyors ensure a balanced distribution of the recyclates. This way these components contribute substantially to the high cleaning degree of the shredded material and thereby make a decisive contribution to the core task of this preparation process.
Metal recycling saves raw material resources. The German steel industry alone uses in excess of 20 million tons of steel and iron scrap for making new products. Steel and non-ferrous metal recyclers make sure that the valuable products are retained in the cycle and raw materials are reclaimed. Under both economical and ecological considerations this is cheaper than primary production in most cases.
The Dutch company HKS Scrap Metals, forming part of the Remondis Group, is among the companies specialised in processing scrap iron, metals and electronic scrap. At their six sites scrap as a secondary raw material of highest quality is reclaimed for sustainable re-use and returned into the material cycle.
The HKS Metals branches are equipped with the latest technical systems for recycling. Three machine-based reclamation methods are in use here: scrap shears, presses and shredders. The scrap shears cut long iron sections to a pre-defined length. The press forms packages to increase the density and ease of transport for the material. The centrepiece of the recycling process, however, is the shredder system, which shreds the recyclates to fist-sized pieces in a first step.
Then a wind sifter separates heavy from lightweight materials. The heavy fraction is subsequently sorted into iron and non-ferrous metals by a magnetic separator.
Here the system components made by CYRUS finally come into play.
Perfect Solution – After HKS Metals in ‘s-Gravendeel (The Netherlands) had replaced its old shredders by modern systems, the upstream vibratory trough conveyors were also put to the test. Key criteria for finding a supplier were after-sales service, technical consulting competence, proximity, quality and speed of response.
Due to the good experience already acquired with CYRUS at other companies in the group they opted for the supplier headquartered in the Northern Ruhr Valley. The scope of the project realised in two stages, included two vibratory trough conveyors specifically designed for the tough conditions in scrap recycling.
The first vibratory trough conveyor is installed downstream from the wind sifter and feeds the first magnetic drum. From there a second vibratory trough conveyor leads to another magnetic drum. Both vibratory trough conveyors equalise the product stream and distribute it evenly for an optimum scrap feed into the magnetic drum. For both trough conveyors the drive consoles were hydraulically riveted with the help of a special connecting system. This maintenance-free connection renders time-consuming and cost-intensive downtimes superfluous. The machines are approx. 5 metres long each and have already conveyed 450,000 tons of scrap.
Good Time Management – In addition to the technical aspects project planning and handling were other key factors that swung the contract: Greek god Odysseus may probably have been able to sail the seas without a map or a compass. After spending ten long years at sea he had acquired the relevant knowledge and the required practical experience needed to sail more or less expertly.
The result – i.e. the destination he arrived at – however, was often not foreseeable and the trip hard to plan. If projects are handled this way, they are exposed to many risks and a “shipwreck” is unavoidable.
CYRUS therefore processed the order for the vibratory trough conveyors with “a map and compass”. In the initial stages of the project the planning teams of KHS and CYRUS already cooperated closely to come up with a tailor-made solution.
After signing the contract in April 2015 further details were specified and stipulated. But not only the technical specificities of the machines to be delivered had to be discussed and/or planned but also the entire project management with all its details. All trades had to work together in a dovetailed manner within a small time window.
After all, there were only 10 months left from the investment decision through the installation of the complete system to the first shredded material.
Positive Customer Feedback – To continue the Odysseus metaphor: with some projects you feel like being caught “between Scylla and Charybdis”. The customer is in a conflict and cannot make up his mind between two apparently equivalent quotes. Regarding this project, however, the total package offered by CYRUS was so compelling that HKS Metals only found positive words about the solutions and experiences: “The approach to solutions already impressed us during the negotiations. Our communication was perfect from the outset because CYRUS employees listened carefully and adjusted the vibratory trough conveyors to our needs,” sums up Herbert Zahn of HKS.
The benefits at a glance:
- Balanced and evenly spread stream of products
- Improved degree of cleaning of the shredded material
- Reduced maintenance through hydraulic riveting
- High consulting expertise of CYRUS employees